How Were Riveted Ships Sealed?
How were ships made watertight back in the old days? Click here to find the fascinating history of riveted hulls.
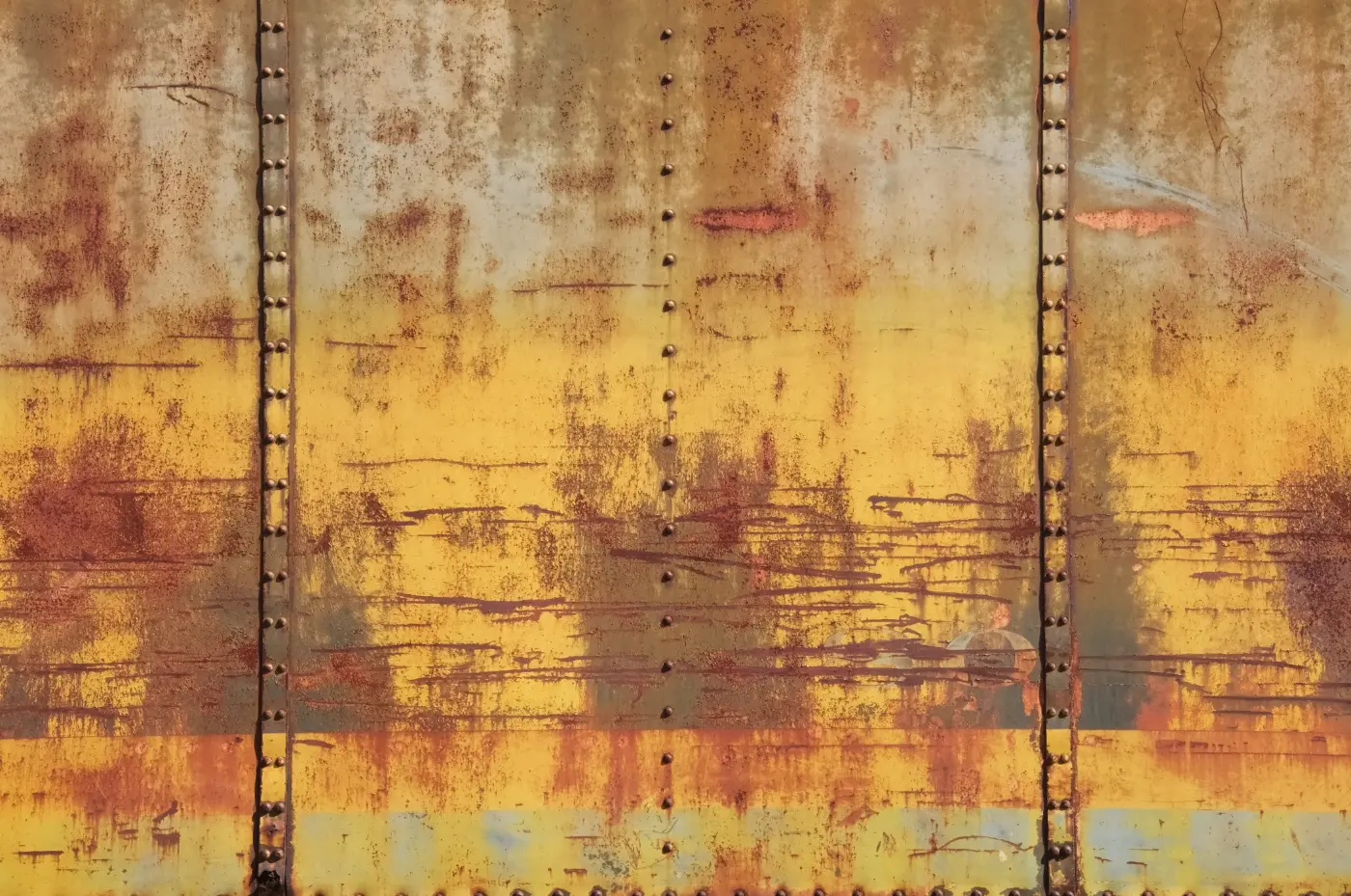
When steel hulled ships used to be riveted, they were naturally watertight thanks to the way the rivets were set. A plate was placed behind the rivet and smashed against it with a hammer to make the metal expand and create a seal.
This technique was far more effective than the pitch caulking performed on wooden ships and remained the standard for sealing ship hulls until around World War II.
In this article, we will discuss in detail the technique used to seal riveted ships and whether or not they still use rivets on ships today. Additionally, we will cover how the old riveting technique compares to the more modern welding technique as well as when welding began to replace riveting.
What Technique Did They Use to Seal Ships in the Old Days?
Once metal ships began to make their debut in the late 18th century to early 19th century, new methods of hull sealants were necessary to ensure that ships were watertight. With wooden ships, the hulls were caulked with thick layers of pitch that would gum up any cracks in the wood and seal it tightly.
However, tar sealant did not work as well on metal ships and they found that, over time, it flattened out and resulted in weak joints. Instead of relying on pitch, shipbuilders took a leaf out blacksmiths’ books and began riveting the hulls together.
By inserting a metal pin through two overlapping pieces of metal and then using the blunt force of a hammer, the flat end of the pin (or rivet) would spread. The expanding metal would fill in any gaps in the metal plates, creating an effective watertight seal.
Later on, rivets were heated up so that the metal was more pliable and created a better seal. Eventually, pneumatic riveters replaced the physical labor of using a hammer.
Do They Still Use Rivets on Ships Today?
Most ships today are not held together with rivets, rather welding is the preferred method. While riveting provided a strong hull, it took a lot of time and skill to line up each individual hole and set the rivets one at a time. Welding took over as the popular method of sealing ship hulls because it is faster and also creates a strong and rigid bond between the metal plates.
There are few companies today that still prefer the riveting method and workers who can rivet are far fewer in number than welders. Certain ships that frequent the Great Lakes and are based in midwestern states such as Wisconsin, Minnesota, and Ohio still employ riveters.
Those who work to restore historical vessels that were built before welded hulls also use riveting to seal the hulls in order to keep the reconstruction authentic. Riveting is considered a unique skill and even after the push to switch to welded hulls, many companies stuck with riveting for a long time before eventually yielding to the modern technique.
How Does the Old Riveting Technique Compare to the Modern One?
The original riveting technique involved heating up rivets and using the physical force of a hammer to smash the flat end of the rivet to displace the metal. As the metal cooled, it would seal the hull plates together. The right amount of force needed to be applied in a timely manner so that the rivet was set before it began to cool.
With the invention of the pneumatic riveter, the force needed to pound a rivet in did not rely on muscular strength but rather mechanics. This helped get the job done faster and was just as effective at creating a waterproof seal for the ship’s hull.
When welding took over as the popular method for sealing a hull, not all companies jumped on board with this technique because it did not prove to be as reliant. In the beginning, welding jobs were not as high quality and led to cracks and fractures in the hull. Over time though, welding surpassed riveting and is now the most used technique.
Both riveting and welding deliver a strong hull and waterproof seal for heavy metal vessels. Welded joints are tight and strong as are riveted joints; however, welding is a faster method and more efficient for shipbuilding nowadays. For example, think how long it took to build the RMS Titanic with three million rivets on the hull!
When Was Riveting Replaced With Welding?
Riveting was the only method for properly sealing a ship’s hull for over a century, until the introduction of welded joints in the 1930s. After World War I, riveted ships began to take a backseat to welded ones so that by World War II a majority of the vessels had welded hulls.
Some companies were not so quick to jump on the welding train and still stuck to riveted hulls. However, the reputation of welded ships took off, and eventually, almost every shipbuilder switched to the more efficient method of sealing hulls.
Now the only companies that still use riveting are a handful in the midwestern United States and historical restoration societies that aim to revive ships from the era when riveting was the only means of sealing a ship’s hull.
Conclusion
Riveted ships were dominant for over a century from the late 18th century when steel hulled vessels first came on to the scene until the early 20th century when welding took over as the preferred method of sealing ships.
Riveted hulls are extremely durable and naturally watertight thanks to the way rivets are pounded through pre-punched holes in the metal sheets that make up the hull. As the rivet is heated up, the blunt force of a hammer – or in later times a pneumatic riveter – would be applied to the flat end of the rivet.
The metal would displace and, as it cooled, seal up the joints of the hull pieces, making it extremely watertight. There was no need for pitch since the metal of the rivet made an excellent seal that could last for decades.